The input data for the blister pack design process are the geometry of the product, the size of the blister pack, the desired number of products per blister pack and the material of the forming foil.
First step is designing the cavity (pocket). We must insure that the cavity is deep enough and that there will be no micropores on the forming foil. Both conditions are very important. If the pocket is too shallow, the product may be damaged during the process of sealing the lidding foil to forming foil. The micropores on the forming foil mean that the product is no longer protected against external factors, such as humidity and contamination for extended periods of time.
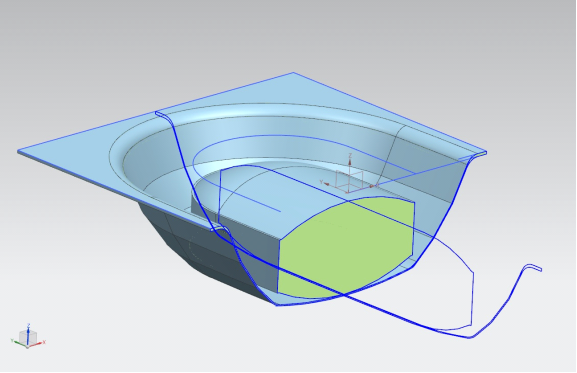
In the second stage the desired number of pockets are distributed on the blister pack. Sufficient intermediate space must be provided for good sealing and there is space left for dating. If there is not enough space the floor plan of the pocket is shrunk. As a rule, the smaller the floor plan of the pocket, the greater the risk of micropores. If desired, perforation and reinforcing ribs can be added. If the desired number of products cannot be placed on the desired blister pack with the certainty that there will be no problems with packaging, a larger blister pack is suggested.
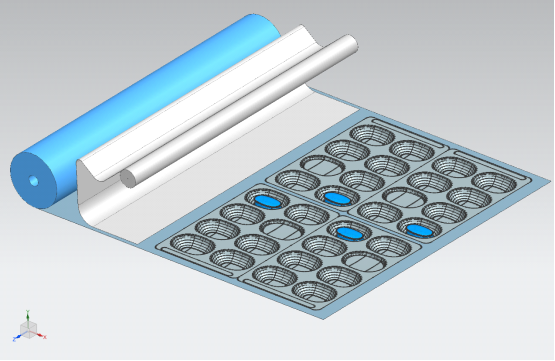